Slash EU CBAM Costs: How Guantong’s Long-Life SCR Catalysts Ensure NOx Compliance
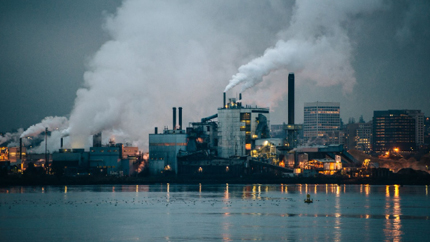
1. Introduction: The Double Squeeze of EU NOx Targets and CBAM Costs
The European Union is tightening its grip on industrial pollution.The Industrial Emissions Directive (IED) mandates a significant 50% reduction in industrial NOx emissions by 2030. Simultaneously, the Carbon Border Adjustment Mechanism (CBAM) is changing the game for global trade, imposing tariffs on carbon-intensive imports.
The Challenge for Exporters:
For Chinese enterprises in sectors like steel, power generation, cement, and chemicals exporting to the EU, this presents a formidable double burden:
- Compliance Costs: Investing in effective emission control systems like Selective Catalytic Reduction (SCR) to meet stringent NOx limits.
- CBAM Tariffs: Purchasing CBAM certificates for every ton of CO? equivalent embedded in their products exported to the EU, directly impacted by energy efficiency and emission control performance.
The Guantong Advantage: Lifespan is Your Leverage
While SCR technology is essential, simply installing a system isn’t enough. The hidden key to unlocking significant, long-term cost savings lies in the lifespan of the SCR catalyst.
We argue that focusing on extending SCR catalyst life through advanced, technology is the most strategic way to:
- Reduce catalyst replacement frequency and associated maintenance costs/downtime.
- Lower the lifecycle carbon footprint of your emission control system.
- Directly slash your CBAM compliance costs.
This article explores how Guantong’s innovative SCR solutions help you navigate these challenges and turn compliance into a competitive advantage.
2. Understanding Industrial Denitrification: Why SCR Technology is Key for CBAM Compliance
Before diving into catalyst lifespan, let’s clarify some basics.
What is Denitrification in an Industrial Context?
Simply put, denitrification is the process of converting harmful nitrogen oxides (NOx) – major air pollutants contributing to smog and acid rain – into harmless nitrogen gas (N?), which makes up about 78% of the air we breathe.Why is denitrification important? Primarily for two reasons: environmental protection and regulatory compliance, especially under frameworks like the EU IED and CBAM.
The Process: How SCR Achieves Denitrification
While natural denitrification occurs in soil and water, industries rely on engineered solutions. The most effective and widely adopted technology for significant NOx reduction in flue gas from power plants, steel mills, cement kilns, and ship engines is
The process of denitrification via SCR involves:
- Ammonia Injection: A precise amount of ammonia (NH?) – often generated safely on-site from urea using a Thermal Decomposition System – is injected into the flue gas stream.
- Catalytic Reaction: The flue gas/ammonia mixture passes over a specialized catalyst.
- Conversion: The catalyst facilitates a chemical reaction where NOx reacts with NH? to produce harmless nitrogen (N?) and water vapor (H?O).
(Equation: 4NO + 4NH? + O? → 4N? + 6H?O and similar reactions for NO?)
Industrial SCR vs. Biological Denitrification:
It’s crucial to distinguish industrial SCR from biological denitrification used in wastewater treatment.
Parameter | SCR Denitrification (Guantong) | Biological Denitrification |
Application | Power plants, steel mills, cement, ships, chemical | Wastewater, agricultural soils |
Reaction Temp. | 150–400°C (Guantong Low-T: 180°C) | Ambient Temperature |
Efficiency | >95% NOx Removal | 30–70% Nitrate Reduction |
CBAM Relevance | Direct Impact on Carbon Reporting & Costs | No CBAM Linkage |
Control & Stability | High, Precise Control | Sensitive to conditions |
Why SCR is the Clear Choice for Industry:
- Compliance Powerhouse: Meets the strictest NOx limits (e.g., <50 mg/Nm3 for EU steel mills).
- Unmatched Efficiency: Guantong’s advanced catalysts, including low-temperature options operating at 180°C, achieve >95% NOx removal while potentially saving energy.
- Operational Stability: Paired with reliable Thermal Decomposition Systems for urea-to-ammonia conversion, SCR ensures consistent performance, unlike sensitive biological methods.
- CBAM Critical: Directly influences the embedded emissions calculations vital for CBAM reporting and cost reduction.
Guantong’s commitment to quality is backed by ISO9001 Certification, ensuring our SCR systems deliver reliable, verifiable emission reductions.
3. The Real Cost Driver: Why SCR Catalyst Lifespan is Crucial for CBAM
Achieving high NOx removal efficiency is just the first step. The economic viability and true carbon impact of your SCR system heavily depend on the catalyst’s operational lifespan. A shorter lifespan significantly inflates both direct and indirect costs.
Data-Driven Cost Reality (Illustrative 20-Year Scenario):
Catalyst Lifespan | Replacements in 20 Years | Direct Cost (Illustrative, CNY 10k) | Embedded Carbon Footprint (Catalyst Production, tCO?e) |
3 Years (Standard) | 6–7 | 1,500+ | ~288 |
5+ Years (Guantong) | ≤ 4 | ~980 | ~192 (Over 30% Reduction) |
Source: Based on Guantong simulations & public data (e.g., EU EDGAR) |
Three Critical Cost Impacts of Short Catalyst Lifespan:
- Soaring Maintenance & Downtime Costs: Frequent catalyst replacement means more planned shutdowns. For industries like steel, downtime can cost millions CNY per day (Example: A steel plant losing ¥2 million/day). Longer lifespan directly translates to fewer shutdowns and lower maintenance expenditure.
- Emission Compliance Risks & Penalties: As catalysts degrade, their NOx removal efficiency drops. This can lead to emission spikes (e.g., exceeding the 50 mg/m3 limit to 80 mg/m3), resulting in non-compliance fines and higher CBAM certificate purchase requirements due to inconsistent performance.
- Amplified Indirect Carbon Footprint: Manufacturing catalysts (especially vanadium-based) is energy-intensive. Producing 1 ton of catalyst can emit around 1.2 tCO?e. Shorter lifespans mean more frequent production, significantly increasing the indirect embedded carbon emissions attributed to your operations under CBAM’s expanding scope.
Focusing solely on initial efficiency while ignoring lifespan leads to unexpectedly high lifecycle costs and carbon liabilities.
4. Guantong’s Solution: Extending Lifespan with ISO9001-Certified Innovation
Guantong tackles the lifespan challenge head-on through meticulous design, advanced materials, and intelligent monitoring, all under rigorous ISO9001 quality control.